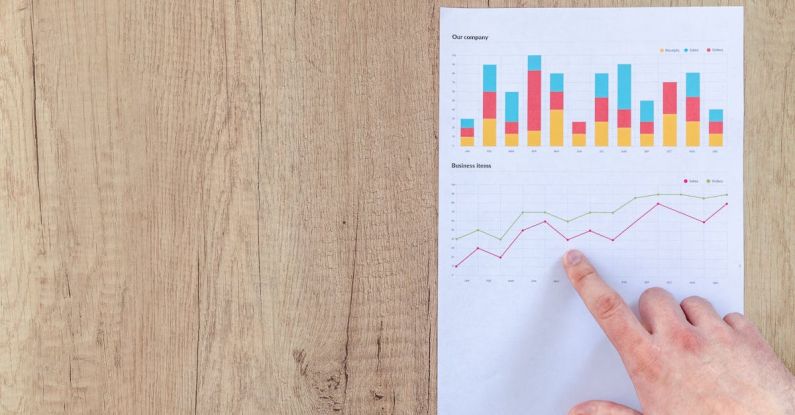
In the fast-paced world of logistics, evaluating performance is crucial for businesses to ensure efficiency, cost-effectiveness, and customer satisfaction. Key metrics play a vital role in providing insights into the effectiveness of logistics operations. By tracking and analyzing these metrics, companies can identify areas for improvement and optimize their processes. Let’s delve into the essential metrics that businesses should focus on when evaluating logistics performance.
**On-time Delivery Rate**
One of the most critical metrics for evaluating logistics performance is the on-time delivery rate. This metric measures the percentage of orders that are delivered on time to customers. A high on-time delivery rate indicates that a company is efficient in managing its transportation and delivery operations. It also reflects positively on customer satisfaction, as timely deliveries are essential for maintaining a positive reputation and building customer loyalty.
**Order Accuracy**
Order accuracy is another key metric that businesses should monitor closely. This metric tracks the percentage of orders that are fulfilled accurately and without errors. Accuracy in order fulfillment is crucial for avoiding costly returns, reducing customer complaints, and maintaining inventory integrity. By focusing on improving order accuracy, companies can streamline their operations and enhance customer trust.
**Inventory Turnover**
Inventory turnover is a metric that measures how quickly a company’s inventory is being sold and replaced within a specific time frame. A high inventory turnover rate indicates that a company is efficiently managing its inventory levels, reducing carrying costs, and minimizing the risk of stockouts. On the other hand, a low inventory turnover rate may signal overstocking or slow-moving inventory, leading to increased storage costs and potential obsolescence.
**Transportation Cost per Unit**
Monitoring transportation cost per unit is essential for assessing the cost-effectiveness of logistics operations. This metric calculates the average cost of transporting goods per unit, taking into account factors such as fuel costs, freight charges, and transportation mode. By analyzing transportation costs per unit, companies can identify opportunities to optimize routes, consolidate shipments, and negotiate better rates with carriers to reduce overall logistics expenses.
**Warehouse Utilization**
Warehouse utilization is a metric that measures how efficiently a company is utilizing its warehouse space. By tracking metrics such as storage capacity, pick rates, and inventory turnover within the warehouse, businesses can optimize storage locations, improve order picking processes, and minimize excess inventory carrying costs. Maximizing warehouse utilization not only increases operational efficiency but also enhances overall supply chain performance.
**Lead Time**
Lead time is the amount of time it takes for an order to be processed, fulfilled, and delivered to the customer. Monitoring lead time is crucial for evaluating the speed and efficiency of logistics operations. A shorter lead time can lead to faster order processing, reduced inventory holding costs, and improved customer satisfaction. By analyzing lead time metrics, companies can identify bottlenecks in their supply chain and implement strategies to streamline processes and reduce lead times.
**Customer Satisfaction Metrics**
Customer satisfaction metrics, such as Net Promoter Score (NPS) and customer feedback ratings, provide valuable insights into the quality of logistics services provided. By collecting feedback from customers regarding their delivery experiences, companies can identify areas for improvement, address issues promptly, and enhance overall customer satisfaction. Positive customer feedback not only reflects well on the company’s logistics performance but also contributes to repeat business and brand loyalty.
**Supplier Performance Metrics**
Supplier performance metrics, such as on-time delivery from vendors and supplier quality ratings, are essential for evaluating the effectiveness of inbound logistics operations. By monitoring supplier performance metrics, companies can ensure a reliable and efficient supply chain, minimize disruptions, and maintain consistent product quality. Building strong relationships with reliable suppliers is crucial for optimizing logistics performance and achieving operational excellence.
**Innovative Technology Metrics**
Innovative technology metrics, such as adoption rates of automation systems, real-time tracking technologies, and data analytics tools, are becoming increasingly important in evaluating logistics performance. By leveraging technology solutions, companies can improve visibility, traceability, and decision-making capabilities throughout the supply chain. Monitoring technology adoption metrics can help businesses stay competitive, drive operational efficiencies, and adapt to the evolving logistics landscape.
**Performance Evaluation Strategies**
To effectively evaluate logistics performance, businesses should implement a comprehensive performance evaluation strategy that combines quantitative metrics with qualitative feedback. By establishing clear performance indicators, setting benchmarks, and regularly monitoring and analyzing data, companies can identify trends, pinpoint areas for improvement, and make informed decisions to optimize logistics operations. Continuous evaluation and adjustment are key to achieving operational excellence and maintaining a competitive edge in today’s dynamic logistics environment.
**In Summary**
Evaluating logistics performance is essential for businesses seeking to optimize operations, reduce costs, and enhance customer satisfaction. By focusing on key metrics such as on-time delivery rate, order accuracy, inventory turnover, transportation cost per unit, warehouse utilization, lead time, customer satisfaction, supplier performance, and innovative technology adoption, companies can gain valuable insights into their logistics performance and drive continuous improvement. By implementing a robust performance evaluation strategy and leveraging data-driven insights, businesses can achieve operational excellence and stay ahead in the competitive logistics landscape.